|
Ucon Compressor Lubricant R-4
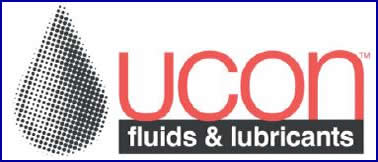
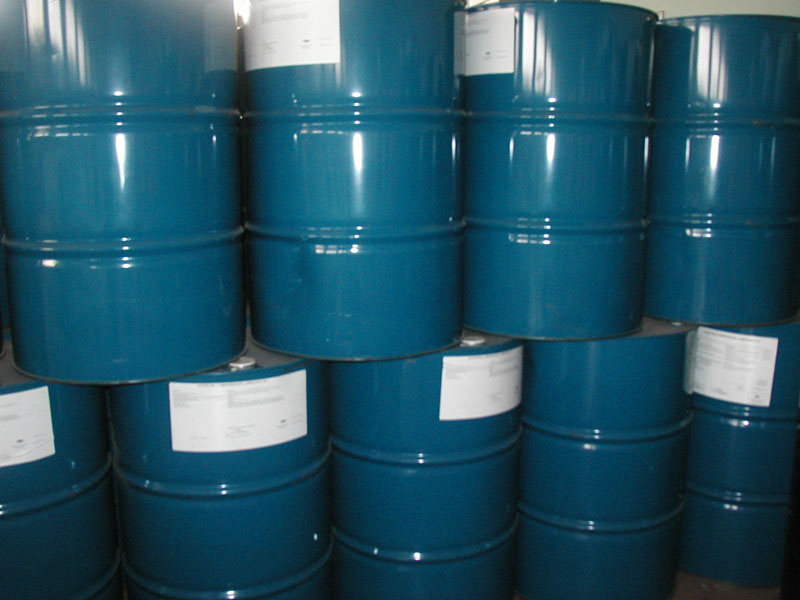
UCON Fluids & Lubricants
Product Description
UCON™ Compressor Lubricant R-4 is a high-performance, PAG-based synthetic lubricant designed for superior cylinder lubrication of reciprocating hydrogen compressors commonly used in refinery processes.
Features and Benefits
UCON Compressor Lubricant R-4 offers compressor manufacturers and users a wide variety of high-performance advantages:
• Compatible with catalysts used in typical refinery processes
• Low hydrogen and hydrocarbon solubility
• Cleanliness: no sludge, varnish, or lacquer formed
• Excellent viscosity index and range
• Low vapor pressure
• Excellent lubricity
• Water tolerance
• Good thermal conductivity
• Excellent compatibility with elastomers
• Reduced maintenance costs
Low Cost/Performance Ratio
The combination of unique physical and performance properties possessed by UCON Compressor Lubricant R-4 results in a very low cost/performance ratio. This lubricant has proven to be superior in performance to both hydrocarbon oils (see Case Studies) and other synthetic lubricants. For example, R-4 exhibits excellent film strength, lubricity at high temperatures, and good viscosity/ temperature characteristics. Excellent performance in protecting compressor parts from scoring and from high rates of wear contributes to significantly increased compressor life. Thus, the equipment manufacturer can offer a more reliable product and the end user benefits from reduced maintenance downtime and lower operating costs.
Typical Physical Properties(1)
UCON Compressor Lubricant
Physical Properties R-4
Viscosity, SUS
at 38°C (100°F)-------------------------------------------------------400
at 99°C (210°F) ------------------------------------------------------84.5
Viscosity, cST
at 40°C (104°F)------------------------------------------------------74.1
at 100°C (212°F)-----------------------------------------------------16.0
Viscosity Index (ASTM D 2270) -----------------------------------231
Pour Point (ASTM D 97), °C (°F)---------------------------------- --41 (-42)
Flash Point, Cleveland Open Cup (ASTM D 92), °C (°F)-----249 (480)
Water Content, max, %---------------------------------------------0.15
Ash Content, max, %------------------------------------------------0.01
Specific Gravity, 20/20°C -------------------------------------------1.041
Pounds per Gallon at 20°C (68°F), (kg/Liter)--------------------8.88 (1.040)
1. The data represent typical physical properties only and should not be construed as product specifications.
Performance
Characteristics
Viscosity Index
UCON Compressor Lubricant R-4 has a high viscosity index of 231, compared to viscosity indexes of 90-95 for mineral oils and 160-170 for competitive synthetics, such as PAO's.
The benefits of high viscosity indexes are graphically illustrated in Figure 1, which compares mineral oil and UCON Compressor Lubricant R-4.
•Lower Pour Point
Pour point is the temperature at which a fluid will not flow, approximately 100,000 cSt (line A). The pour point of the high viscosity index UCON Compressor Lubricant R-4 is lower than that of the same ISO viscosity grade mineral oil.
•Easier Low-Temperature Start-up
At a given start-up temperature (line B), the higher viscosity index of the UCON Compressor Lubricant R-4 affords easier start-ups and handling because its viscosity is lower than that of the lower VI mineral oil.
•Higher Viscosity at High Temperature
If equipment runs hotter than expected (line C), the high viscosity index of the UCON Compressor Lubricant R-4 provides higher viscosity for better lubrication of valuable equipment than the lower VI mineral oil.
Solubility
The solubility of hydrogen in UCON Compressor Lubricant R-4 is very low, as shown in Figure 2. This means that any reduction in lubricant viscosity due to gas dissolution in lubricant is minimal. Therefore, since UCON R-4 maintains its viscosity in contact with hydrogen, it provides thicker lubricant films (film thickness being proportional to viscosity0.7) and better lubrication than other hydrocarbon and synthetic lubricants. The benefits to the user are efficient lubrication, reduced downtimes, longer run times between maintenance schedules, and increased equipment life. In short, UCON Compressor Lubricant R-4 provides a low cost/performance ratio.
Figure 1 • Performance Benefits of High Viscosity Index (VI): UCON Compressor Lubricant R-4 vs. Mineral Oil
Figure 2 • Solubility of Hydrogen at 50°C (122°F) in UCON Compressor Lubricant R-4
Clean Operation
UCON Compressor Lubricant R-4 is made from polyalkylene glycol (PAG) basestocks. It does not decompose under typical compressor operating conditions. Should some degradation occur, PAG decomposition products are soluble in UCON CompressorLubricants and therefore do not tend to separate in the form of sludge or contribute to generating varnish or lacquer. Consequently, equipment runs very clean for long periods.
Furthermore, UCON PAGs are excellent solvents and are very effective in removing dirt from compressor parts. The exceptional cleanliness that results from using R-4 translates into longer equipment life and longer run times between maintenance shutdowns. The net result is economical, trouble-free compressor operation.
Low Vapor Pressure
UCON Compressor Lubricant R-4 has an inherently low vapor pressure. Lubricant losses into the process gas are minimal, resulting in low lubricant make-up costs and low lubricant carryover to downstream processes. Therefore, the amount and frequency of lubricant top offs are reduced, helping keep lubricant usage to a minimum.
Elastomer and Coatings Compatibility
UCON Compressor Lubricant R-4 is compatible with a variety of elastomers and coatings(see Table 2).
Catalyst Compatibility
A key feature of UCON Compressor Lubricant R-4 is compatibility with catalysts used in typical refinery processes, such as reforming and hydrotreating. R-4 is made from a consistent, high-quality polyalkylene glycol and contains no additives that can poison catalysts ordinarily used in these processes.
In independent testing conducted by UOP, a major licensor of refinery processes, UCON Compressor Lubricant R-4 was found to be compatible with catalysts used in the reforming of naphtha and hydrotreating processes. On the other hand, competitive mineral oil and diester lubricants generally contain contaminants (e.g., metals) that poison catalysts. The fear of catalyst incompatibility has forced many refinery operators to go to nonlubricated compressor designs that typically require a very high degree of maintenance.
UCON R-4 offers an attractive alternative, combining the benefit of excellent lubrication with catalyst compatibility. It can also be used to lubricate nonlubricated compressors, reducing the amount of maintenance needed.
Changeover Procedure
Any time a lubricant change is made, care should be taken to assure the system is properly prepared according to good operating standards. At a minimum, we recommend old lubricant be drained, the system cleaned, any seals and elastomers inspected, and filters replaced or screens cleaned before the UCON Compressor Lubricant is installed. System cleaning may be necessitated by the build-up of sludge and/or varnish in old systems.
Physical wiping or flushing with a small amount of UCON Compressor Lubricant may be required if residual contamination is expected. New units require the removal of preservative or coating fluids in similar fashion.
After installing the UCON Compressor Lubricant, adjust lubricators to deliver the manufacturers' recommended rate of lubricant. Check filters or screens frequently during the early stages of operation since UCON Compressor Lubricants will likely loosen residual sludge, varnish, and paint.
Table 2 • Elastomer and Coatings Compatibility
Recommended Not Recommended
Elastomers |
Viton A |
Buna S |
|
Kalrez |
Hycar |
|
Butyl K 53 |
Natural Black Rubber |
|
Buna N |
Hypalon |
|
Natural Gum Rubber |
|
|
Neoprene |
|
|
EPR Chloro Sulfonated |
|
|
Polyethylene |
|
Thiokol 3060 Polysulfide
Coatings ------------- Catalyzed Epoxy-Phenolic ---------Alkyd
Modified Phenolic
Case Study 1 Problem
Two hydrogen compressors (see details below) had never pumped capacity while using a premium (ISO 150) petroleum lubricant for cylinder lubrication at eight pints per day compressor lube rate. In addition, rings and packing suffered extremely high wear and frequent breakage. Six overhauls per year were required over five years to clean and remove wear debris from compressor and downstream components and maintain capacity. Many lubrication and operating parameters were varied, unsuccessfully, over the five years.
Solution
Over a period of 36 months, the use of UCON Compressor Lubricant R-4 for cylinder lubrication eliminated abnormal ring and packing wear at lubricant rates of only 0.875 pints per day per compressor. Wear was eliminated, along with the subsequent need for frequent overhaul. No ring breakage occurred at the lower lubrication rates. At the scheduled 12- month inspection, there were no signs of abnormal wear. Overhauls are now scheduled at two-year intervals.
Details
Equipment: Cooper Bessemer FM-3, 10 1/2-in stroke compressors, 438 rpm, 455 HP, 3 cylinders, 3 stages.
Case Study 2 Problem
Compressors (see details below) in a Gulf Coast refinery, used in make-up hydrogen service, had been lubricated with a diester lubricant. The hydrogen contained particulates in the form of iron sulfide and iron chloride corrosion products. Compressor discharge valve plate movement was being restricted by a very viscous, tenacious sludge formed by the mixture of the particulates and the diester cylinder compressor lubricant. Similar problems occurred with the piston rings. Frequent valve and piston ring changes were required to keep the compressor operating with acceptable discharge temperature and throughput.
Solution
The diester cylinder lubricant was replaced by UCON Compressor Lubricant R-4. R-4's excellent solvency prevented accumulation of deposits on the discharge valves, piston rings, and cylinder. Sludge formation on the discharge valves has been virtually eliminated, and the valves operate freely. Piston ring and rider band wear was also reduced. Although compressor problems still occur with hydrogen system upsets, compressor operation has improved during normal operating periods, with a reduction in the need for valve, ring, and rider band changes.
Because UCON Compressor Lubricant R-4 is compatible with catalysts used in reforming and hydrotreating units, there was no problem concerning catalyst damage caused by any lubricant carryover.
Results
Savings of 50 percent in total maintenance costs were realized in the first year in which UCON R-4 replaced the diester lubricant. R-4 played a major role in achieving these savings by eliminating the need for numerous shutdowns, disassembly required for overhaul, and a reduction in component replacements. Furthermore, the calculation does not include the value of increased on-stream time after conversion.
Details
Equipment: Three Cooper Bessemer KM-2, two-stage, 327 rpm, 14-in stroke, 1800 bhp, 185 psig suction, 1440 psig discharge hydrogen compressors.
Product
Stewardship
Dow encourages its customers and potential users to review their applications from the standpoint of human health and environmental aspects. To help ensure that Dow products are not used in ways for which they are not intended or tested, Dow personnel will assist customers in dealing with environmental and product safety considerations. Dow literature, including Material Safety Data Sheets, should be consulted prior to use.
|
|